چکیده مطلب
باستان فلز شناسی / آرکئومتالورژی
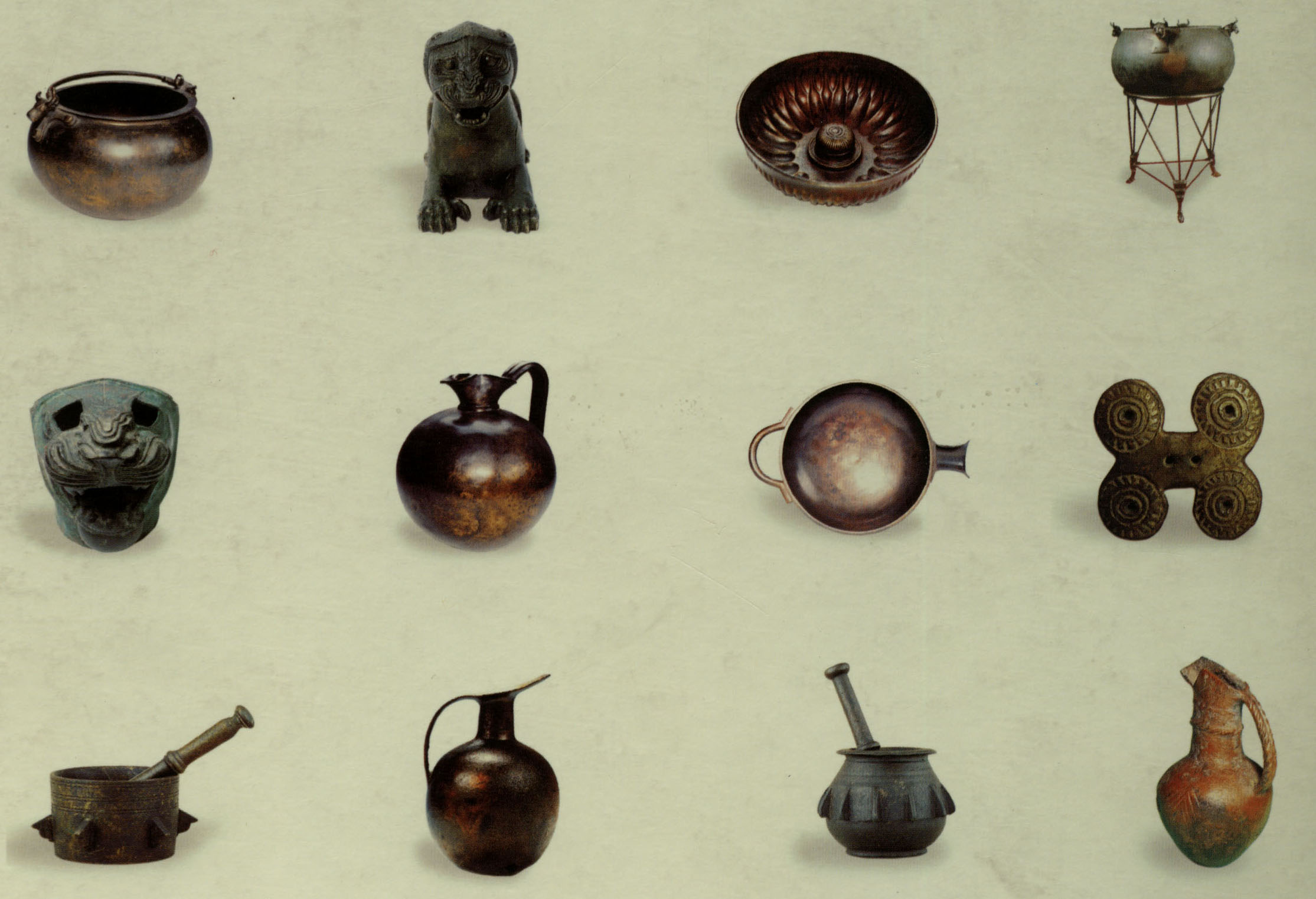
این تعریف که « متالورژی یکی از قدیمیترین هنرها و یکی از جدیدترین علوم است »، بخوبی تاریخچه طولانی و موثر رشته متالورژی را بیان میکند. از زمانی که بشر فلز را شناخت، متالورژی را بهعنوان یک هنر فرا گرفت. این علم، فرآوری مواد معدنی از کانههای آنها – جداسازی از سنگ معدن، ذوب، تصفیه و تولید […]
مشروح مطلب
این تعریف که « متالورژی یکی از قدیمیترین هنرها و یکی از جدیدترین علوم است »، بخوبی تاریخچه طولانی و موثر رشته متالورژی را بیان میکند. از زمانی که بشر فلز را شناخت، متالورژی را بهعنوان یک هنر فرا گرفت. این علم، فرآوری مواد معدنی از کانههای آنها – جداسازی از سنگ معدن، ذوب، تصفیه و تولید شمش بهبود خواص و تهیه آلیاژها و فن کار بر روی فلزات و شکل دادن آنها را در بر میگیرد. صنعت متالورژی در جهان از دیرباز بهعنوان صنعت مادر شناخته شده، با پیشرفتهای روز افزون تکنولوژی، نقش آن آشکارتر میگردد.
اصطلاحات و مفاهیم تخصصی متالورژی
با در نظر گرفتن این مطلب که هر علمی واژگان و مفاهیم و اصطلاحات تخصصی خود را دارا می باشد. و صاحبان این علوم برای بیان مفاهیم فنی از این اصطلاحات استفاده می نمایند و از جانب دیگر مفاهیم مورد ذکر در نزد باستان شناسان – به دلیل خلا مباحث متالوژیکی در واحد های درسی دانشگاهی رشته باستان شناسی – ناآشنا و غریب می باشند، لذا ضرورت دانسته شد تا برخی از این مفاهیم با رعایت ترتیب الفبا و به اختصار تعریف گردد:
1- آلیاژ
مخلوطی از دو یا چند فلز، در علم متالورژی به حاصل ترکیب دو فلز به روش گداختن در هم ذوب شده، بصورت ریخته گری آلیاژ می گویند. بعنوان مثال نقره غالبا با درصد کمی از مس آمیخته شده و این امر به ایجاد ویژگی های فیزیکی مطلوبتر و سود اقتصادی بیشتر منجر می شود.( گانتر و جت، ترجمه: حیدرآبادیان، 1383: 359).
2- استحصال فلزات
بطورکلی هرگونه تحصیل فلز از مواد معدنی در شکل خاک یا سنگ معدن را با روش حرارت دهی یا بدون حرارت استحصال فلزات می نامند. بدین ترتیب در این روش برای بدست آوردن برخی از فلزات از مواد معدنی موجود در طبیعت الزاما حرارت و کوره مورد نیاز نمی باشد و همین امر وجه تمایز استحصال فلز از ذوب فلز می باشد. و بعنوان مثال می توان به استحصال دانه های طلا از میان ماسه های سطح رودخانه یا استحصال مس با طریقه شکستن سنگ معدنی و آزاد سازی گرانول های مس، اشاره نمود.
3- الکتروم
آلياژ طبيعي طلا و نقره معمولاً سفيد يا نقره اي رنگ و حاوي حدود 40% نقره.
4- بوته ذوب فلز
ظرفی به گونه های مختلف در شکل پیاله یا لیوان، در اندازه های متفاوت. که در دوران گذشته اغلب از جنس سنگ و گاهی اوقات از جنس چینی و سرامیک و سفال و یا فلزات مقاومتر ساخته می شد و دارای دسته ای ثابت یا جدا شونده برای استفاده در زمان جاری نمودن فلز مذاب بود. ( تصویر 2)
5- تشويه
عمل تشويه شامل اکسایش جزئي سولفیدهای پرعيار حاصل از فلوتاسیون و حذف جزئي گوگرد از آنها به شكل SO2 است. اين كار توسط واكنش كاني پرعيار شده با هوا در دماهايي بين 500 تا 700 درجه سانتي گراد در كوره هاي تشويه اجاقي انجام مي شود. محصول كوره تشويه کلسین ناميده مي شود و مخلوطي از اكسيدها، سولفاتها و سولفيدها است.
فرآيند تشويه معمولاً خود سوز است و جريان گاز SO2 توليد مي كند. از عمل تشويه معمولاً در كوره هاي ذوب شعله اي استفاده مي شود كه هدف اصلي از آن خشك كردن و گرمايش بار كورة شعله اي با استفاده از حرارت واكنشهاي گرمازاي تشويه است. محصولات گرم كوره تشويه نسبت به كاني پرعيار شده خيس و سرد به انرژي كمتري براي ذوب نياز دارند، به طوري كه عمل تشويه باعث صرفه جويي قابل ملاحظه اي در مصرف سوخت و افزايش آهنگ ذوب مي شود.
6- ذوب فلز
عملیات آماده سازی و ذوب سنگ معدن حاوی فلزات گرانبها، بعنوان فرایند قبل از عملیات قال گذاری طی مراحل زیر انجام می پذیرد:
الف – ابتدا سنگ معدن پودر شده، لیتارژ ذغال ( بعنوان احیا کننده ) و مواد کمک ذوب – شامل کربنات سدیم و بوراکس (اسید بوریک) کاملا باهم مخلوط گردیده درون بوته ذوب ریخته می شوند. روی این مخلوط به منظور جلوگیری از اکسید شدن مواد محتوی آن بوسیله قشری از نمک طعام پوشانیده می شود.
ب- بوته آماده را در یک کوره که قبلا به حرارت 900 درجه سانتیگراد رسیده قرار می دهند، در کوره را می بندند و حرارت آنرا به 1050 درجه سانتیگراد می رسانند.
ج- در چنین حرارتی یکسری فعل و انفعالات شیمیایی بین مواد کمک ذوب، لیتارژ، زغال و سنگ معدن صورت گرفته طی آن لیتارژ به سرب احیا می گردد. کربنات سدیم و بوراکس نیز با ترکیبات اسیدی و قلیایی موجود در سنگ معدن ترکیب شده سرباره را بوجود می آورند.
برای رسیدن به تکنولوژی ذوب فلزات رسیدن به فناوری ایجاد حرارت با درجات بالا ضرورت دارد. در جعفرآباد شوش – در هزاره چهارم ق.م. – ، نمونه هايي از كوره هاي سفال پزي با درجه حرارت بالا كه نشان پيشرفت تكنولوژي در آن زمان بوده را مي توان ديد. احداث اينگونه كوره ها مقدمه اي براي ساخت كوره هاي مناسب تري براي ذوب و توليد فلزات گرديد اما حرارت توليد شده در اين كوره ها بيش از 600 تا 700 درجه سانتي گراد نبوده است كه اين دما براي ذوب مس كافي نيست. در حالي كه در كوره هايي با اين ميزان حرارت مي توان سنگهاي اكسيد مس را احيا نمود. بنابراين مي توان نتيجه گرفت كه عمليات ذوب مس در ابتدا از سنگهاي مس دار آغاز شده است و مس خالص در اين دوران تنها از طريق چكش خواري شكل داده شده است.
اولين كوره هاي احيا و ذوب سنگ مس گودالهاي ساده اي بودندكه در آنها سنگهاي اكسيدي مس همراه با زغال چوب ريخته مي شد و براي بالا بردن حرارت در اين گودالها به كمك دم يا راه هوا درون كوره دميده مي شده است. آنچه محصول اين عمل بوده نوعي آلياژ است زيرا همزمان با احيا سنگ معدن مس سنگهاي ديگري كه حاوي فلزات ديگر بود احيا شده و در تركيب با فلز قرار گرفته و آلياژ حاصل مي شد. اما آلياژي كه کاملا مورد نظر بشر نبوده و نسبت به خواص و ويژگي هاي آن اطلاعي نداشته است. اين آلياژ در ته كوره جمع مي شده و نقطه ذوبي كمتر از مس خالص داشته است. براي شكل دهي به آن با عمليات چكش كاري بر روي آن اقدام مي شده است. اما رفته رفته بشر به فكر افتاد راهي پيدا كند كه بتواند اين فرآورده را به صورت بهتري استحصال نمايد. لذا از بوته در اين مقطع زماني – هزاره هفتم ق.م. – استفاده گرديد. بدين منظور قطعات سنگهاي مس را قطعه قطعه به ابعاد 2 تا 3 سانتي متر در مي آورند سپس آنها را با زغال چوب مخلوط كرده و در گودال هايي به قطر 75 سانتي متر و عمق 25 تا 120 سانتي متر – بر اساس شواهد باستان شناسي- مي ريختند و روي آن را آتش زدند. پس از آتش زدن زغال چوب در سطح خارجي گودال هواي لازم براي احتراق زغال در كوره دميده مي شد. در صورت تامين حرارت لازم مس همراه با ناخالصي هاي فلزي ديگر قطره قطره در كف كوره جمع شده و پس از سرد شدن منجمد مي شد. در مورد پالايش بهتر مس و خلوص سازي آن دو نظريه وجود دارد:
1- پس از طي مراحل ذكر شده پالايش مجدد در كوره هاي ديگر انجام مي گرفته و هواي لازم جهت سوختن زغال به روشهاي پيشرفته تر از طريق دم دستي تأمين مي شده است و در بالاي كوره بادگير قرارمی گرفته است براي پالايش مس از بوته هاي سفالي كه از خاك رس ساخته شده بود، استفاده شده است.
نظریه دیگر آنكه قطعات مس خرد شده يكباره در درون كوره ای که بوته در کف آن قرار داشت، قرار می گرفت و در نتیجه مس پالایش شده در کف بوته جمع می گردید.
برخي صاحب نظران معتقدند اين كار به صورت دو مرحله اي انجام مي شده زيرا در اين حالت وارد كردن كاني گرم شده در كوره سبب افت دما در اين مرحله نمي گردد و نهايتاً بازدهي بهتري خواهد داشت.
« فلزکاران و هنرمندان با گداختن سنگ مالاشیت و اکسید آهن و طلا و نقره در آتش، این فلزات را ذوب می کردند، اما چون کار آنها پایه نظری نداشت، علت سیلان را نمی دانستند، با اینحال فلزکاری و از جمله شناخت اکسید های مختلف، کشف معادن، استخراج، احیای فلزات و تکنیک زرگری، مسگری، چکش کاری، ریخته گری، لحیم کاری، ملیله کاری، ترصیع و قلمزنی بر گرفته از هنرمندان باستانی است که قوه خلاقه خود را در ساخت آثار هنری عالی و جاودان به منصه ظهور رساندند.» ( کامبخش فرد ، 1380 : 16 ).
7- ذوب مات
هدف از ذوب مات تهيه فاز سولفيدي مذاب شامل تمامي مس موجود در بار و فاز سرباره مذاب بدون مس است. مات متعاقباًٌ براي تشكيل مس حفره دار ناخالص تبديل مي شود. – اكسيد مي شود- و سرباره مرحله ذوب مستقيماً يا بعد از مرحله بازيابي مس دور ريخته مي شود. عمل ذوب توسط ذوب تمامي بار كوره در دمايي حدود 1200 درجه سانتي گراد معمولاً همراه با روانساز سليسي انجام مي گيرد. سليس، آلومين، اكسيدهاي آهن، آهك و ساير اكسيدهاي جزئي سرباره مذاب را تشكيل داده مس گوگرد آهن اكسيد نشده و فلزات قيمتي مات را تشكيل مي دهند. سرباره سبك تر از مات و در آن تقريباً غيرقابل حل است و به سهولت از آن جدا مي شود.
يكي از هدف هاي مهم ذوب مات توليد سرباره اي جداشدني شامل حداقل ميزان مس است. اين كار توسط اشباع تقريبي سرباره از سيليس – كه باعث عدم حلاليت مات سرباره مي شود- از طريق گرم نگه داشتن كوره به حد كافي به طوري كه سرباره مذاب و سيال باشد و با اجتناب از شرايط اكسيدي اضافي عملي است. اين شرايط اخير براي كاهش هرچه بيشتر تشكيل منيتيت جامد – Fe3 O4 نقطه ذوب 1597 درجه سانتي گراد- الزامي است چرا كه شرايط چسبنده اي ايجاد مي كند و مانع جدا شدن مات از سرباره مي شود. عمل ذوب در كوره هاي سنتي صورت مي پذيرد.
ذوب مات شامل ذوب كاني پرعيار شده يا كاني پرعيار شده اي كه تا حدي تشويه شده باشد در دماي 1150-1250 درجه سانتي گراد جهت توليد دو فاز مذاب جدا شدني – غيرقابل انحلال- است. سرباره – اكسيد- و مات غني از مس (سولفيد) محصول اصلي فرآيند ذوب مات CuS-FeS – مس 65-35 درصد- است كه براي فرآيند تبديل و توليد مس حفره دار مورد استفاده قرار مي گيرد. سرباره مذاب مستقيماً يا پس از انجام يك مرحله بازيابي مس جدا مي شود و بايد حد امكان عيار مس آن كم باشد. تشكيل دهنده اصلي بار آهن و اكسيد مس وآهن و سولفيد مس است. بار شامل اكسيدهايي از قبيل Al2O3 و CaO و MgO و عمدتاً SiO2 نيز هست كه در كاني پرعيار شده است.
محصولی از استحصال مس از سنگ معدن.
وجود دارند يا به عنوان روانساز به آن اضافه مي شوند. آهن مس گوگرد اكسيژن و اين اكسيدها تشكيل دهنده شيميايي و فيزيكي سيستم مات-سرباره را كنترل مي كنند. (جدول 1)
قالکاری ( قال گذاری)
« فن قال گذاری از مهمترین و قدیمیترین روشهای تولید نقره و سایر فلزات گرانبها از سنگ معدن در دوره های پیش از تاریخ بوده است. استفاده از این فن برای هزاران سال با تغییرات اندکی ادامه یافته است. این شیوه علاوه بر تولید فلزات گرانبها، جهت بازیافت این فلزات از قراضه فلزات و اشیا فلزی ساخته شده و نیز عیار سنجی بکار می رفته است( Bayley & Eckstein , 1995 ) اساس روش قال گذاری بر استفاده از خواص شیمیایی ( و تاحدودی فیزیکی ) سرب، نقره، طلا و سایر عناصر استوار است. بدین ترتیب که سرب مذاب بعلت جاذبه شدید شیمیایی نسبت به فلزات گرانبها، بعنوان جمع آوری کننده آنها بکار می رود. » ( نوکنده و نظافتی، 1382: 22 ).
فلز كاري باستاني ( آهنگری )
« فلز کاری ( = آهنگری = متالوژی ) : باید دانست کلمه فلزکاری شامل معانی فن استخراج فلز، ذوب فلز، ریخته گری و آهنگری است. طبق مدارک تاریخی ایرانیان از جمله نخستین مردمانی بودند که بعلت دسترسی به کان های بزرگ و غنی مس در نقاط مختلف کشور این فلز را می شناختند و احتمالا اولین تولید کننده، مصرف کننده و صادر کننده لوازم مسی در دنیای پیش از تاریخ بودند. از قرائن وآثار بدست آمده کاوش های آزمایشگاهی و تجزیه کربن 14 آثار کشف شده معلوم می شود که ایرانیان دست کم از 5000 سال ق.م مس را ذوب و آنرا تلخیص میکردند. در خراسان احتمالا از هزاره چهارم، در ایلام از هزاره سوم، در کردستان و لرستان و آذربایجان از 3500 ق.م این فلز را برای ساخت لوازم زندگی و ملزومات جنگی و آثار هنری به کار گرفته اند. معادن مس در فلات قاره ایران در کوههای سهند، قره داغ، انارک، کوههای قفقاز، دامغان، سرچشمه در نزدیکی کرمان، بافق، طالمسی ( مخفف طلا و مس ) در کویر لوت، نایین، تل یحیی و زاگرس بطور پراکنده بهره برداری شده اند.» ( احسانی ، 1382 : 51).
فن شناسی اشیا فلزی
به طور خلاصه فن شناسي، شناسايي مواد متشكله، شيوه ساخت، شكل دهي و تزئين يك شيئ است. در فن شناسي تخصصي تر، لازم است اطلاعات كامل خلاصه و طبقه بندي شده در خصوص مواد تشكيل دهنده، تاريخ ساخت، نحوه شكل دهي و وجود مرمتهاي قبلي ارائه داد. فن شناسي در كنار آسيب شناسي جهت درمان اثر تاريخي از اهميت ويژه اي برخوردار است.
کانه
کانه جسمی است که در طبیعت یافت میشود و میتوان از آن یک یا چندفلزرا آنچنان که مقرون به صرفهباشد استخراج کرد. بعبارت ساده تر هر ماده معدنی که بطور اقتصادی قابل بهره برداری باشدکانه نامیده میشود. هر کانه متشکل از تعدادی کانیاست که حداقل یکی از آنها کانی با ارزش موجود در ماده معدنی است و در حقیقت ماده معدنی برای دستیابی به آن کانی استخراج میشود، سایرکانیهای متشکله ماده معدنی را کانگمی می نامند.
معدودی از فلزاتی که واکنش پذیری آنها کم است به شکل عنصری خود درطبیعت یافت میشوند و برای چند تا از آنها “کانه خالصطبیعی” مهمترین منبع فلز را تشکیل میدهد. بیشترین تناژ فلزات از اکسیدها – خواه کانههای اکسیدی ، خواه اکسیدهای فلزی که از برشته کردن کانههای کربنات یاسولفید تولید میشوند، بدست میآیند.کانههای سیلیکات در طبیعت فراوانند. ولی استخراج فلزات از سیلیکاتها مشکل است و هزینههای چنین فرآیندهایی مانع ازانجام کار میشود. در نتیجه فقط فلزات کمتر متداول بطور صنعتی از کانههای سیلیکاتبدست میآیند. کانیهای فسفات بطور کلی نادرند و در غلظتهای کم یافت میشوند. تعدادیاز فلزات بصورت ناخالص در کانههای خالص طبیعی دیگر یافت میشوند، بطوری که هر دوفلز از یک عمل صنعتی بدست میآیند. برای مثال، فلز کادمیم به عنوان محصول فرعی در تولید روی بدست میآید.کانهها به هنگام استخراجعموما مقادیر متغیری مواد نامطلوب – مثلسیلیس،خاکرسوگرانی- که ” هرزه سنگ” نامیده میشوند، به همراه دارند. غلظت فلزمورد نظر باید به اندازه کافی بالا باشد تا استخراج آن از نظر شیمیایی امکانپذیر واز نظر اقتصادی قابل رقابت باشد. بر روی کانههای دارای غلظت پایین از فلز در صورتیکار میشود که بتوان آنها را بوسیله فرآیندهایی به نسبت آسان و ارزان قابل استفادهنمود، یا این که محصول فلز نایاب و پرارزش باشد. غلظت لازم از یک فلز به فلز دیگرتغییر زیادی دارد. برایآلومینیومیاآهن این غلظت باید 30% یا بیشتر و برایمس ممکن است 1% یا کمتر باشد.
کانه آرایی ( پرعیار سازی )
در بيشترموارد، مواد معدنى پس از استخراج مستقيما قابل استفاده نبوده و بايد پر عيار شوند. پرعيارسازى همان کانه آرايى مواد معدنى است که با جدا کردن مواد بى ارزش يا باطله از مواد با ارزش صورت مى گيرد و باعث بالا رفتن عيار و در نتيجه کيفيت ماده معدنى مى گردد.کانه آرایی در واقع مجموعه عملیاتی است که بر روی ماده معدنی، پس از استخراج انجام میشود تا آن ماده را قابل مصرف کند.
آخرین نظرات